Airport expansions are one of the most complex challenges in modern infrastructure construction. The demanding nature of ongoing operations, unique security requirements, the concentration of transport links, and the diversity of operating and social stakeholders massively constrain available options and allows room for error.
Learning from the best
Project teams, their designers, and their supply chains need to build and maintain high levels of integrated project performance to avoid significant delays and cost overruns. However, modern methods of construction combined with the precise management style seen in daily airport operations provide an environment in which this excellence can be developed and sustained.
One of the largest airport owners in Europe has been developing and refining these approaches over the last twenty years as they have totally rebuilt their portfolio of terminals and structures – all whilst maintaining the operations of some of the busiest airports in the world. Their projects team have been leaders in the adoption of Lean, as well as the use of large-scale offsite modular construction, supply-chain integration, owner control of risk, and early stakeholder involvement.
Driving executional excellence
When having to build a new elevated pier as part of one terminal expansion – construction surrounded by operating runways – everything was done to produce a modular design of repeating 9m x 22m x 18m sections. Sections that avoided any wet concrete above ground and offered an erection sequence that compressed trades, minimised lifts, optimised use of structure as a safe construction platform and minimised high-cost / high-risk on-site hours. Significant effort was put into the design phase, using a fully integrated design team combining architects and engineers with all suppliers (from steel and glass to tiles and lighting) to optimise the structure for performance, construction, operations and cost. The final design was then prototyped at full scale, on the edge of the airfield, in part to confirm performance but more to allow the construction teams to develop the fastest build sequence with learnings and modifications being made and re-tested before the final design and build was released for construction. The goal for each trade – one day to install one section. This was a significant acceleration of a large pier build, resulting in substantially reduced disturbance, risk and costs. Thereby, demonstrating the benefits of combining lean, offsite and modular at scale.
The need to develop a culture of openness
The focus on de-risking the delays and associated costs by controlling and increasing predictability – critical in an operating airport – is also an area where modern performance transparency is starting to show valuable benefits to both owners, contractors and suppliers. Digital tools are now being employed to more efficiently and effectively track daily progress in construction and pre-construction, and then make this status clear to all dependent parties. The effectiveness of one of the key features of Lean – Frontline Pull – is amplified when the teams supplying the frontline can see and build trust that the pull is really required. This transparency is not a simple switch to achieving performance. Projects need to develop a culture of openness where early transparency of emerging risks is an opportunity to address them together rather than failures to be judged. Teams that have embraced this mindset report that they quickly switch from avoiding negative events to improving expected performance.
Developing these integrated teams across a rolling programme of projects like this has been a critical success factor for many large capital projects businesses across the built environment in infrastructure, hospitals and major retail brands. The integration of a small group of key contractors is often core to this. Successful central project teams have worked hard to change traditional confrontational relationships into partnerships that allow owners to reduce capital intensity of projects whilst increasing predictable profits for their key contractors. By working consistently with a selected group of contractors, portfolio owners can ensure that these contractors have a forward flow of work in return for above target performance on cost, quality, time and/or innovation. In turn, this performance can be incentivised with higher margins or increased volumes. By partnering for the long term and for performance, these groups have demonstrated that win-win in construction is possible far more often history might have us think.
Strong owners teams both deliver and own the results
There remain many instances of delayed and over-budget projects across industry and infrastructure but, even with their significant complexities, major airport programmes can and are brought in on time and on budget with performance improving project by project. It takes strong owners teams that recognise and proactively manage out the high complexity of their unique environments. These owners teams make the best use of modern technologies and approaches, significantly integrating their supply chains early and reallydriving whole project performance every day. They truly own the result with their key partners.
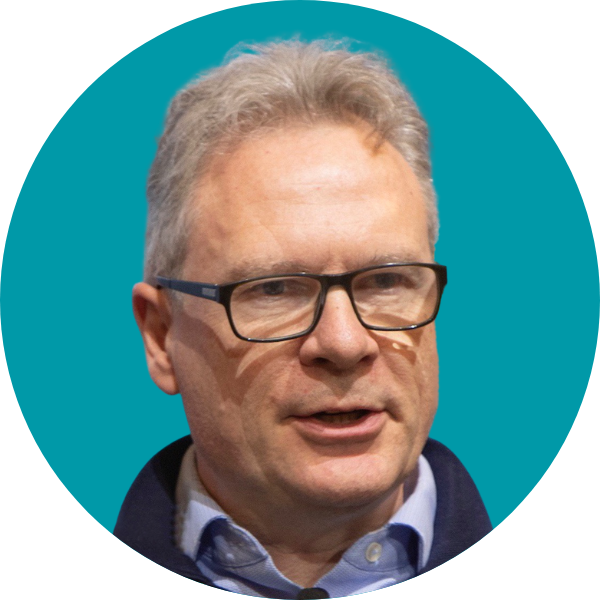
Guy Turner
Guy Turner co-leads Partners in Performance’s Global Capital Practice focused on working with owners and contractors to build integrated project execution teams that deliver high performance every day. “Every project can come in ahead of schedule and under-budget”
Linkedin