Improvements in automation technology and the constant push to increase efficiency are driving the adoption of automation in the mining industry. Globally, mining operations are at various stages of maturity on the automation scale from remote operation centres to fully automated systems.
Autonomous Trucks have been used across sites to increase productivity, improve safety and lower costs. Increased productivity is realised through higher utilisation from reduced crew change-over and reduced overhaul intervals. Improved safety is realised through reduced human error and lower costs are achieved through reduced labour expenditure.
Larger mining companies are leading the way with this technology with Rio Tinto launching its Mine of the FutureTM initiative in 2008 with a target of 140 autonomous trucks by the end of 2019. Since the initial implementation, Rio reported autonomous trucks to be 12% more productive than the manned fleet and load and haul costs reduced by 13%. Further savings are expected as data analytics is used to define a predictive maintenance program.
In many cases an automation solution does not deliver the full benefit initially estimated. This is due to poorly executed implementation and slow ramp up of the new system. Getting the expected results from an autonomous fleet requires not only a technical component, but also a cultural shift within the organisation. The most likely reason for slow-ramp up times is the shortage of skilled autonomous technicians, developers and support staff.
Further to this, management commitment, planning and focus on the implementation can hold back project delivery. To ensure maximum and timely impact of implementing an autonomous fleet, these considerations must be well thought out through the planning and implementation of the project.
Readying operations for autonomous haul trucks
Before a mine can be ready to deploy the use of autonomous systems, there are four layers of planning that must be completed:
- Mine planning design
- Engineering design management framework
- Information systems architecture
- Project deployment
- Project commissioning.
Mine system infrastructure and operational processes need to accommodate autonomous systems that require new approaches for material movement. The mine design needs to be set up for autonomy, including making changes to work areas and traffic management.
A strong design management framework will reduce safety risks as well as minimise breakdowns and production delays. This management framework needs to be updated to capture the changes brought by an autonomous haul fleet.
The three information architecture subsets applied to autonomous systems are:
- Business
- Data
- Technology
It is important to note that implementing automation to an efficient operation will marginally improve that efficiency as effective systems and processes are in place. Implementing automation to an immature operation may not gain the expected returns and perhaps the money is better spent getting the basics in place prior to automation.
Three improvements that will add value before, during and after truck automation are:
- Improving haul roads
- Leveraging big data
- Uplifting maintenance maturity.
Running surface improvements on haul roads reduces rolling resistance and fuel usage. Also, improving intersection design and adding superelevation to corners can reduce cycle time of trucks. As autonomous trucks are introduced, road widths can be decreased due to the precision of the autonomous vehicle path.
Taking control of a mine’s data can drive value as it transitions to an autonomous fleet. Analysing operational data to identify factors that contribute to best and worst operational performance scenarios can inform a new and adaptable operating model for the haul fleet. Further, analysing maintenance and condition monitoring data can inform an efficient predictive maintenance strategy reducing parts usage and increasing overhaul durations.
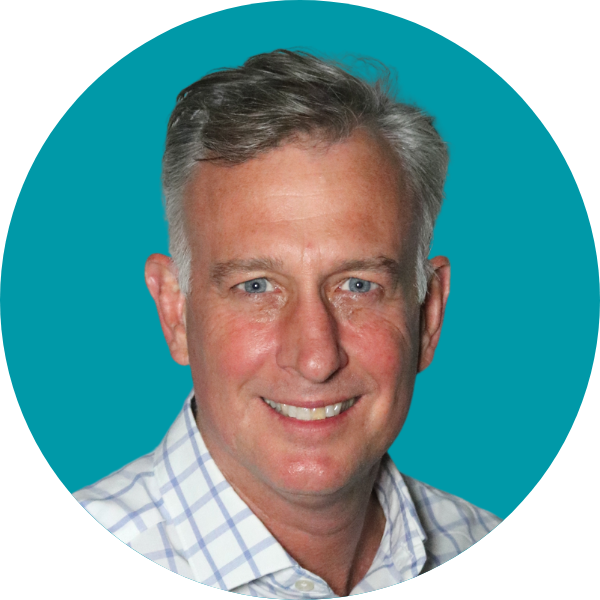
Michael Huggins
As the head of Partners in Performance’s Australian practice, Michael has brought over two decades of experience to his clients and colleagues by transforming industrial companies. Specifically, he sets up businesses to drive accountability and results.
Linkedin